As a kid, I occasionally had the pleasure of catching episodes of The A-Team when I was allowed to stay up late. The show had plenty of action and comedy, at a level ideal for a ten-year-old boy. But my favorite part was always the inevitable scene where the team would harvest a bunch of scrap metal parts or an old van, and start cutting, grinding and welding them together into a new contraption. Cut in the form of a montage with the A-team theme song playing in the background, Mr. T and his teammates would send showers of sparks and precise beams of flame shooting around their workshop as they brilliantly created some new weapon or vehicle that was critical to succeeding in their mission.
Since then, I’ve always wanted to gain the magical Power over Metal that the A-team had. But even as my woodworking experience grew, my metalworking skills did not advance beyond using a hacksaw to cut the odd long bolt down to size. Metal was a forbidden material – unknown, too hard to cut and too fussy to join together to allow for practical use.
That all changed in the year 2005, when I was building my first custom house. It was a modernist design in a new urban neighborhood, and the architect I had hired took advantage of that freedom to plan some really cool details into the place. Exposed steel railings, bolts, and brackets were to be blended in next to loads of wood and natural stone, highlighting the airy and sun-filled living spaces. It all sounded great, until I sent the design over to a Boulder-based metalworking contractor, and he sent me back a quote for $15800.00, about four times my budget of $4000 for that part of the project.
“Damn!”, I said, “If this guy is billing out his metalworking time at $75.00 an hour, that’s a sign that I need to finally learn the craft myself. How hard can it be?”
So began my saga of metalworking, and in the years since then I have profited immensely from the new skill. Tens of thousands of dollars have been saved and earned, and many interesting things have been invented that I never could have created from wood alone.
After building the steel staircase railing systems at that house, I was immediately recruited to do a similar railing system for someone’s rooftop patio. Then I started creating garden accents like steel gates and unusual plant holders. I used the expanded set of ideas to design even more metal architectural details into my second custom house project. Then I went on to more relaxing projects: welding up an enormous steel lumber rack and permanently attaching it to a 1984 Nissan pickup truck, creating structural parts to help straighten up the sagging foundations and floors of historic houses, making signs for Mrs. Money Mustache’s real estate sales business, building some of my own workout equipment, and even making a custom shower curtain rod for the new shower in the Foreclosure Project house. Right in the middle of making this article, my garage door opener ripped its attachment bracket in half due to improper installation, and I was able to fix it with.. welding!
Besides being an enjoyable skill to learn, welding and metalworking gives you an aura of mystery due to the fact that hardly anyone knows how to do it these days. I could barely spark up my welding machine when working in the posh custom home neighborhood without catching the attention of passers by who would walk over and say, “You’re a WELDER?? Could I have your business card? Because I have a project I’d love you to take a look at.” Another one of my work crew with welding skills was recruited away from underneath me, to spend the winter on a Florida Key, crafting an elaborate balcony and patio system for a financial tycoon’s new seaside mansion.
Because of this shortage and appeal to high-end clients, I believe that metalworking would make an ideal side-hustle for a person who already enjoys building things. It would also make a great business for a younger person who wants to earn enough between college semesters to get out of school debt-free. Heck, with the right business skills, metalworking is a way of getting a professional-level income without the need for a college degree. Higher hourly rates, sparse competition, and interesting projects all seem to be common among self-employed welders. And with very little training and no licensing required, it’s easy to pick up.
So just in case this appeals you, now or sometime in the future, I’m going to plant a Welding Recipe in your head. You can use it today, or you can file it away for later when you quit your day job.
Stuff You Need:
Just as I summarized in an earlier article on getting started in carpentry, the basics of creating cool things from steel are the identical for those in woodworking: Design, measure, cut, attach.
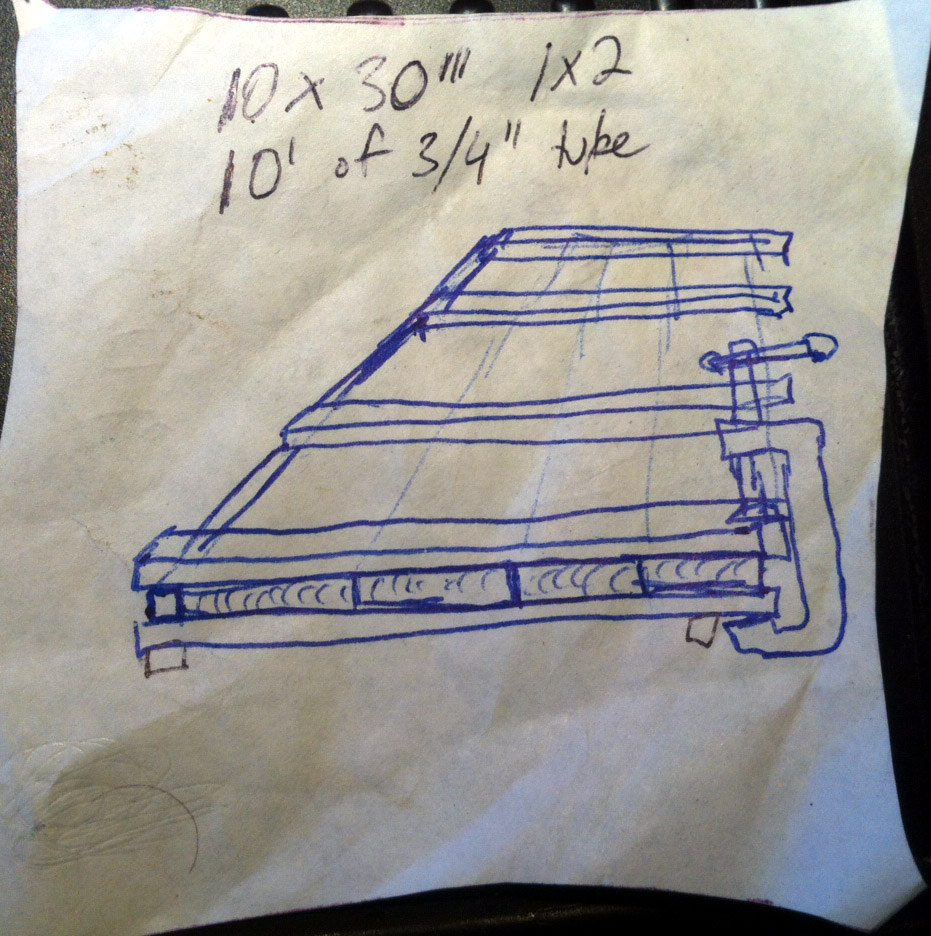
Here’s a hasty design sketch I made for a metal table for clamping together long boards to speed the process of gluing them into large sheets for furnituremaking. I ended up building this thing, picture later in this article.
The design stage for steel is slightly different, just because you don’t have as much freedom to carve and trim things on a table saw like you do with wood. So you focus on mostly straight stock widths, cross-cut at various angles, and attached together in simple arrangements. With basic metalworking tools, you won’t be making yourself a curvaceous supercar. But you CAN certainly make a nice Mad-Max-style dune buggy, go-kart, or even a bike or trailer.
In exchange for the reduced cutting flexibility, you get enormously greater strength: you can zap two 1/8″ thick inch pieces of steel plate together for 15 seconds on the welder, and the resulting joint will already be strong enough to support a small truck.
With steel, you buy long tubes of the material by specifying wall thickness, shape, and size. I drew this sketch for you of the most common types:
A few basic metal pieces can be found right in the hardware section of Home Depot and Lowe’s. But for serious projects, you’ll want to find a metal shop. Look up “welding” in your local business directory, and you’ll end up at a friendly old sheetmetal building in the industrial section of town where the guys have grease on their cheeks and awkwardly peck away on a beige 486 running Windows 95 to ring up your order. There you’ll probably find the best prices on steel, and will be available in lengths of up to 24 feet. I get my raw materials at “Mountain View Welding”, shown at left.
With knowledge of design and materials, the last step is the tools. They’re surprisingly simple:
A Grinder:
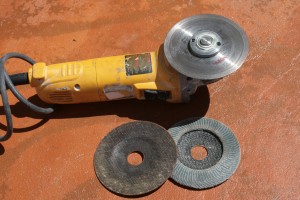
My grinder has the concrete-cutting blade on it in this picture, metal cutting is lower left, sanding wheel is lower right.
This is the official Mr. T. tool. Its a dead-simple handheld rotary tool that simply spins a 4.5″ disc around extremely fast (about 11,000 RPM). The disc has rough parts that hit the steel at high speed and cause it to break off in dust-sized pieces. Because of the energy involved in each tiny collision, the broken fragments are instantly heated to white-hot temperature, so they appear as a glorious shower of sparks that shoots across your workshop, lighting it up like a KISS show. The sparks aren’t as dangerous as they look – they will bounce off a flannel shirt and extinguish themselves before they even hit the floor. But you still don’t want to grind steel in the presence of exposed gasoline or other flammable things. Also, don’t use your grinder with the blade guard and side handle detached like I do. It’s much more dangerous like that.
By fitting different discs to the grinder, you can cut, smooth, and polish steel. You can also throw on a diamond blade and cut through rocks, tile, and concrete as if they were butter. Or a sanding wheel to destroy any thickness of old paint on wood within seconds. So it’s a versatile tool. Dangerous too – keep those fingers away from the 11,000 RPM.
Cost: $30 – $75 … Harbor Freight Tools Example, Home Depot Example
A Metal Chop Saw:
Like a single-purpose stationary grinder with a massive 14″ cutting wheel, this low-tech behemoth can make rapid and fairly clean cuts across the pieces of tube steel shown in my diagram above. It clamps the tube in place, and you lower the cutting head down to make the chop. There is an angle setting, allowing you to make corner joints and other useful cuts.
Cost: $100-$200 … HFT Example, HD Example
A Welder:
The king of your metalworking kit is of course the welder. There are many types available, and I agonized over them for quite a while before deciding. But I’ll save you the hassle and just tell you the best type for high rewards and low effort: a 120 volt wire-feed flux core welder.
The way this welder works is that a thin wire of special metal alloy is slowly fed through the gun-style handle that you hold in your hand when you squeeze the trigger. Simultaneously, a giant (but very low voltage) electric current is passed through the tip of the metal alloy and forced to jump into the piece of metal you want to weld. The electricity jumps across the gap, creating a spark that is hot enough to melt steel, and then a tiny pool of liquid metal forms at the junction of the two pieces you are joining. It’s a mixture of the metal of the two pieces, plus a bit of your alloy, plus some “flux” in the wire which helps keep the reaction smooth.
Cost: $200-$450 … HFT Example , Lowe’s Example
Safety Equipment:
Welding with this type of equipment creates a bunch of jumping hot sparks. They burn for longer than the grinder sparks, so you need to do it on a non-flammable surface like a concrete patio or a piece of metal or cement-based tile backerboard set up on sawhorses to form a convenient work bench.
You also need a pair of puffy heatproof welding gloves to protect your hands from the sparks and ultraviolet light from the welding spark (I actually got a mild sunburn after welding all day once with some exposed skin).
And most importantly a welding visor. This is simply a plastic shield that keeps sparks off off your face, which has a lens as dark as about 20 pairs of sunglasses stacked together. The dark lens allows you to look at the welding spark and the molten steel (about as bright as staring directly into the Sun), comfortably, to control your work easily. In the olden days, these visors were permanently dark, meaning you couldn’t see your work until you actually started the welding spark. Nowadays, the visors are “auto-darkening”, which means the glass is clear until it detects bright light. At that point, a liquid crystal layer in the glass is instantly charged, turning it black so your eyes do not even notice an instant of brightness. When you stop the bright spark, the glass instantly lightens again.
Cost: about $60 – HFT Welding Visor, Gloves
And of course, these things can usually be found on Craigslist as well – I just provide the new product links for comparison so you know the base value.
Technique:
We’ll leave the details of designing a specific metal thing for another article, but let’s just focus on how to join two pieces of steel together.
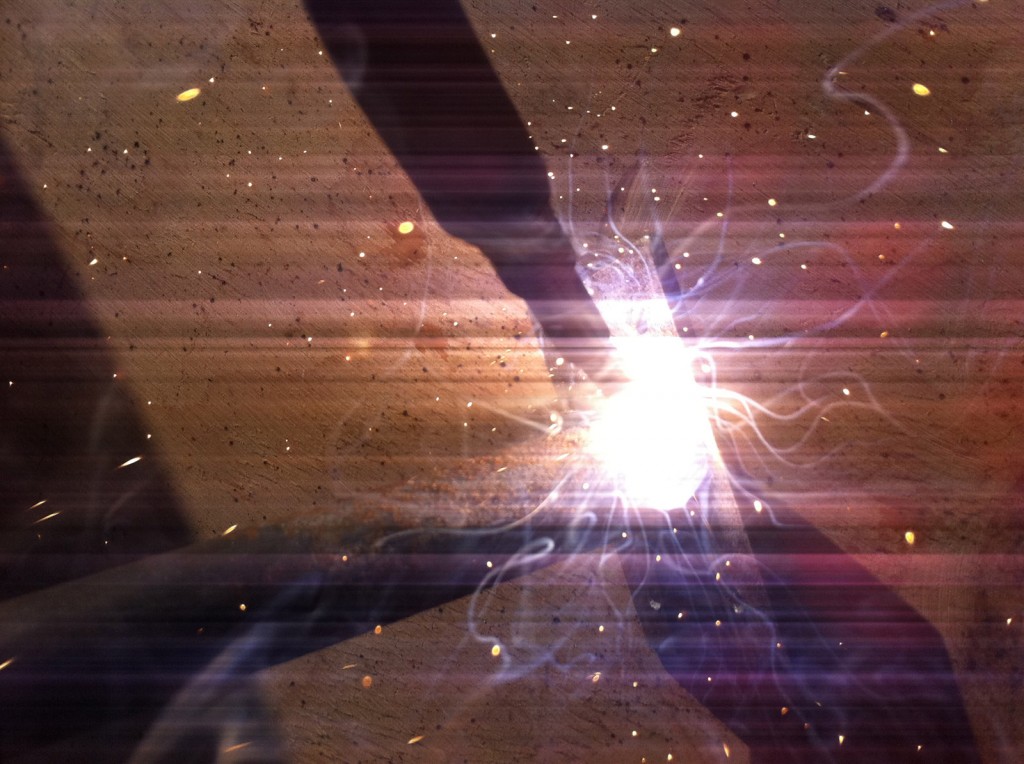
- Clamp ’em – you want your pieces to be locked into exactly their final angle, since as soon as you weld them, they will be joined forever. So you set them in the appropriate positions on your work table, and clamp them down, using spacers and blocks of wood or metal as needed to get the right position.
- Connect the neutral wire somewhere – welding requires you to form a complete electrical circuit from the machine, through your work, and back to the machine again. So you clamp its alligator clip to part of your work.
- Lower your visor, position the gun, brace yourself and squeeze the trigger. You’re welding! Sparks are flying, a quiet sparkling firecracker sound emerges from your work, and a small amount of hot smoke is swirling about. You see the small orange pool of molten steel forming at the tip of your gun. You keep squeezing, and slowly move the gun, which makes the pool of liquid metal spread along the joint. The area you left behind rapidly cools, and becomes a strong bond. The more slowly and accurately you control your liquid pool, the better the quality of your welding.
After your joint is complete, it will need quite a few minutes to cool back down before it’s safe to touch (since you had it at over 2000 degrees F while welding). But even before cooling, the joints can be smoothed with an abrasive wheel on the grinder, or buffed to a nice shine with a spinning wire wheel brush (on grinder or cordless drill). Here’s an example of a rough joint just after I welded it, and the same joint after a minute or two with the grinder:
After the welder and grinder work is complete, metal projects can be painted just like a car – with automotive primer in spray or brush-on form, and then any sort of finish. Or, they can just be left to form their own protective layer of rust, a look that is deliberately cultivated in many modern outdoor steel projects.
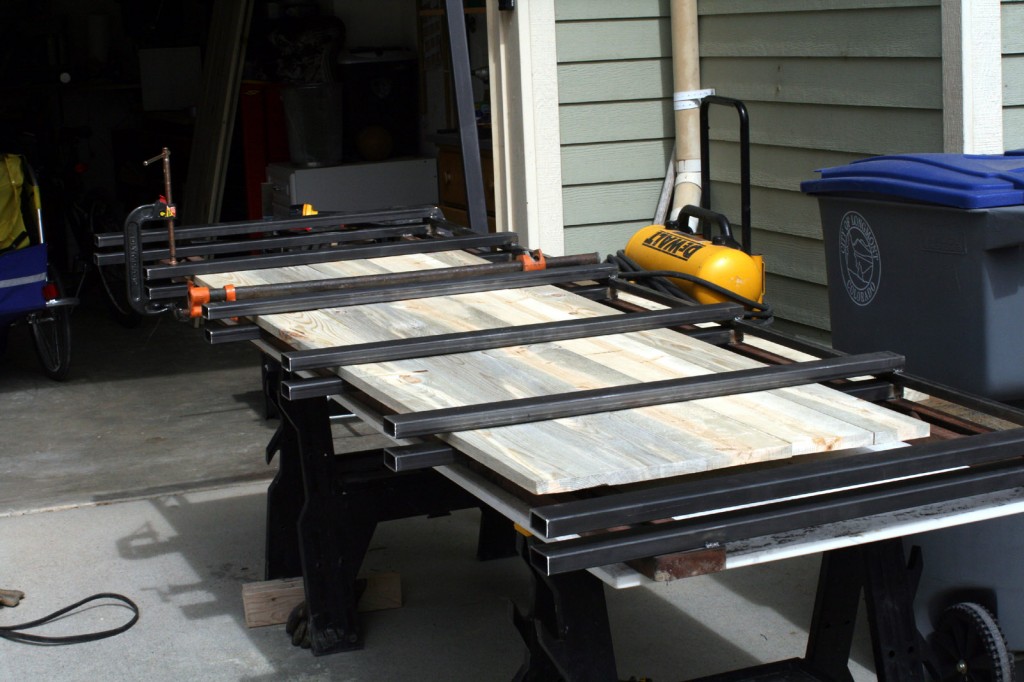
Here’s that clamping table, converted from sketch to reality. It is squeezing together a bunch of formerly-crooked 1×6 beetle-kill pine boards to become the lid of a casket for the company “Nature’s Casket“. Note the 1″x2” rectangular tube steel.
After understanding these fundamentals, there are finer points that can be polished up by searching around on YouTube. But as with many of my introductory articles, my goal here is to show you that this new skill is fun, relatively easy and inexpensive to get started with, and for the right people, a profitable addition to a self-sufficient lifestyle.
Leave a Reply
To keep things non-promotional, please use a real name or nickname
(not Blogger @ My Blog Name)
The most useful comments are those written with the goal of learning from or helping out other readers – after reading the whole article and all the earlier comments. Complaints and insults generally won’t make the cut here, but by all means write them on your own blog!